Finding ways to increase spray efficiency
Increasing spray efficiency is all about maximising impact and minimising losses. This blog covers ways to improve spraying efficiency through better mixing and batching setups, managing water quality, and minimising spray drift.
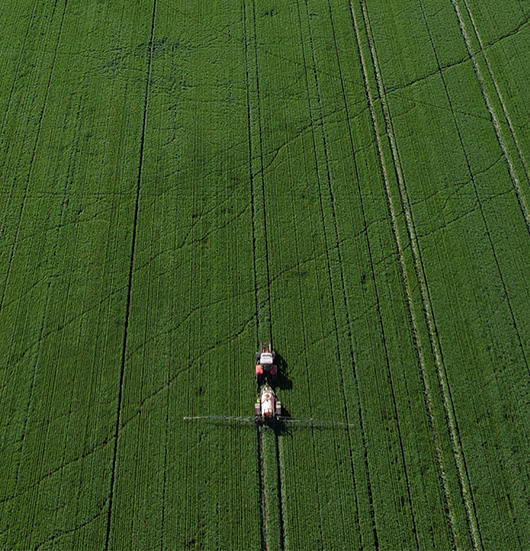
Key messages
- Improving spray efficiency is more than just reducing chemical use – it’s about achieving the best agronomic outcomes while saving time, reducing chemical waste, and protecting the environment.
- As input costs rise, minimising waste when filling and making each spray application count has never been more important.
- Incorporating closed batching systems or automatic fill equipment into your spray setup can improve safety, accuracy, and efficiency.
- Reduced exposure to chemicals is a key advantage of closed batch mixing systems.
The spray application process comes with lots of individual steps and therefore lots of opportunities for improving efficiency. This blog covers key considerations for boosting spraying efficiency through better mixing and batching setups, managing water quality, and minimising spray drift.
Logistics matter (it all adds up)
The spray mixing and application process offers many opportunities to increase labour, machinery, and pesticide efficiencies.
To work out areas where efficiency gains can be made in your system, consider your spraying rate in hectares per hour and consider how much time is spent folding and unfolding your boom. There’s also time spent travelling from paddock to the filling station, time spent measuring chemical, mixing the tank and filling with water. It may also be valuable to compare working machine hours vs idle hours if running a system such as JD ops centre.
Time savings – the value of mixing equipment
Reducing travel time between fill points will boost operational efficiency. A mobile water tank or chemical mixing unit can help keep the sprayer moving, not waiting.
However, there are some key factors to consider before deciding which mixing equipment will work best for you. The size of chemical containers you normally handle, solubility of products used, tank size of sprayer, cleaning and decontamination needs and road access will all be factors in designing an effective system.
Loading your tank: safe, fast, accurate
Incorporating closed batching systems or automatic fill equipment into your spray setup can greatly improve safety, accuracy, and efficiency.
Closed systems reduce operator exposure to chemicals and help prevent spills.
Automatic fill equipment eliminates the need for manual measuring and minimises human error. They are also easy to use — often as simple as entering the area (hectares or total litres), application rate, and product rate per hectare, and the unit will load the exact amounts into your sprayer—which is ideal for liquid products.
Examples of batching equipment available for purchase in Australia include from: Ideal Sprayers, Ag Spray Centre, AJS machinery, McIntosh and Son, SprayCentre, Scudagchem, Burando Hill.
Water quality
Water makes up 95–99% of a typical spray mix, yet is often overlooked as a factor in spray efficiency. Poor water quality can reduce the efficacy of herbicides, insecticides, and fungicides.
Hard water (often caused by high concentrations of dissolved calcium and magnesium) can bind with products like glyphosate, reducing their effectiveness. It’s recommended to use water conditioners or ammonium sulfate (AMS) when hardness exceeds 150 ppm.
High pH (alkaline water) can cause alkaline hydrolysis, breaking down sensitive chemicals like dimethoate or 2,4-D. Test pH using strips or digital meters and adjust with acidifiers or buffers if pH is above 7.
Organic matter and sediment, including dirt, algae, and residues can block filters and nozzles. Always use clean, filtered water, and regularly clean tanks to prevent buildup.
Application: minimising spray drift
Spray drift doesn’t just waste product—it can damage off-target crops, threaten sensitive areas, and reduce compliance.
To reduce the risk of spray drift, consider the following management strategies:
- Nozzle selection: Use coarse to ultra-coarse droplet nozzles (e.g., air induction).
- Boom height: Keep booms at the recommended minimum height above target (usually 50 cm).
- Weather awareness:
- Avoid spraying in wind <3 km/h (inversion risk) or >15 km/h.
- Avoid temperature inversions, which often occur at dawn or dusk.
- Buffers and additives: Use buffer zones and consider drift-reducing agents in sensitive locations.
Check your local weather conditions via Riverine Plains Weather Stations.
Summary
Investing time into your spray setup and preparation can pay dividends in the paddock. By improving batching and mixing systems, managing water quality, and reducing drift, you’ll achieve more effective control of weeds, pests, and diseases—and get better value from every litre of product used.
Resources
Mixing and batching chemicals a key to spray efficiency (GRDC)
Mixing, filling and transfer systems (GRDC)
Author
Lynn Macaulay
Member Engagement Officer Bachelor of Agriculture and Farm Business Management
2 July 2025
NEWS
Keep up to date with what's happening across the Riverine Plains.
-
Sustainability
-
Climate